Essential Guide to Grain Storage Temperature for Optimal Harvest Preservation
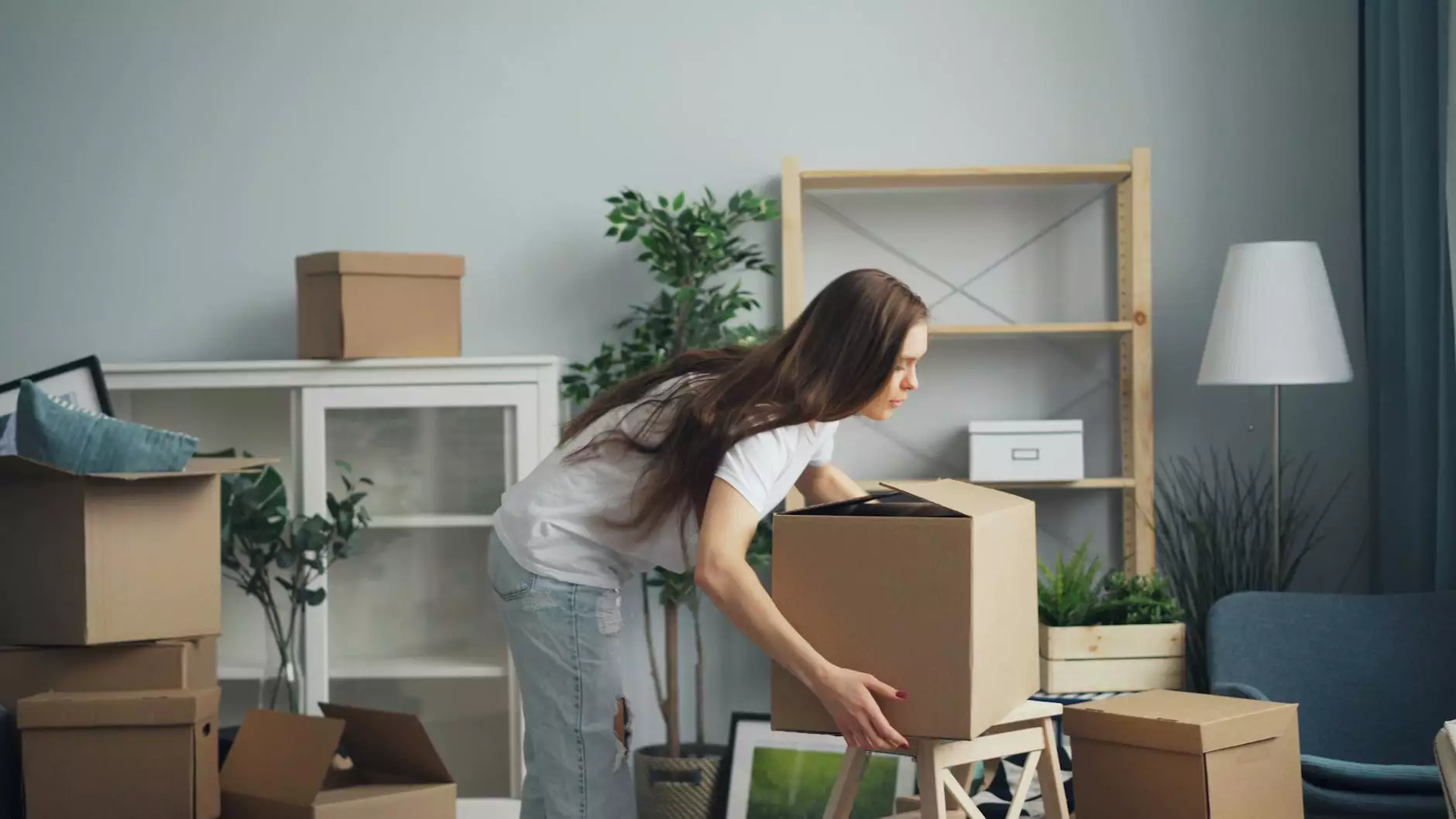
In the agricultural sector, managing the grain storage temperature is crucial for maintaining the quality and longevity of harvested crops. Whether you are a farmer, a grain elevator operator, or involved in the agricultural supply chain, understanding how temperature affects grain storage can make a significant difference in preventing spoilage and loss of yield. This article delves deep into the importance of maintaining the right temperatures in your grain storage facilities, providing insights and strategies for optimal results.
Understanding Grain Storage Temperature
Grain, like other perishable products, is sensitive to its storage environment. Temperature affects the moisture content of grains, their respiration rates, and the development of mold and pests. Proper temperature management not only extends the life of grains in storage but also preserves their nutritional value and marketability.
The Impact of Temperature on Grain Quality
When it comes to grain storage temperature, maintaining the right levels is fundamental. Here’s a detailed look at how temperature affects grain quality:
- Moisture Regulation: High temperatures can increase the moisture evaporation rate, leading to dryer grains, which can be beneficial or detrimental depending on the grain type and storage conditions.
- Pest Control: Certain temperatures can deter pest activity. Warmer conditions can accelerate pest growth, while cooler storage can help inhibit their reproduction.
- Mold and Spoilage: Elevated temperatures can lead to chemical reactions that promote mold growth and spoilage. Keeping grains at a stable, cooler temperature helps maintain quality.
- Nutritional Integrity: High storage temperatures can degrade grains nutritionally, reducing their value both for livestock feed and human consumption.
Ideal Temperature Conditions for Various Types of Grains
Different grains have specific temperature ranges that are ideal for storage. Below are recommended temperature conditions for popular grains:
1. Corn
For corn, the optimal storage temperature is between 45°F to 50°F (7°C to 10°C) if moisture content is around 15%. Corn that is stored at lower temperatures can maintain its quality longer, making it less susceptible to spoilage.
2. Wheat
The best storage temperature for wheat is also within the range of 45°F to 50°F (7°C to 10°C). Like corn, cooler conditions help prevent mold and pests.
3. Soybeans
Soybeans prefer a slightly warmer environment. Ideal storage temperatures range from 50°F to 60°F (10°C to 15°C), depending on moisture content. However, reducing the temperature below 50°F can be beneficial during warmer months.
4. Barley
Barley can be stored at temperatures similar to wheat and corn, specifically 45°F to 50°F (7°C to 10°C). This helps in maintaining the barley’s quality for malting and brewing purposes.
Technologies and Equipment for Temperature Control
To effectively manage grain storage temperature, various technologies and equipment can be employed. Here are some recommended solutions:
1. Aeration Systems
Aeration systems help in controlling the temperature and moisture levels within your grain storage facilities. These systems circulate air through the grains, helping to dissipate heat that may accumulate from environmental factors or biological activity.
2. Temperature Monitoring Systems
Modern storage facilities employ temperature monitoring systems that provide real-time data on the conditions of stored grains. These systems can alert operators if temperatures exceed recommended levels, allowing for immediate intervention.
3. Insulated Storage Units
Utilizing well-insulated storage facilities can significantly reduce temperature fluctuations. Insulated bins and silos help maintain a steady internal climate, protecting grains from external temperature changes.
Best Practices for Managing Grain Storage Temperature
Implementing best practices for monitoring and managing storage temperatures can lead to long-term benefits. Here are some practical strategies:
- Regular Monitoring: Conduct regular checks of grain temperatures using thermometers or thermal imaging devices. This helps in spotting anomalies early.
- Frequent Aeration: Implement a schedule for aerating stored grains, particularly during temperature spikes, to ensure uniform temperature distribution.
- Prompt Cleaning: Regularly clean storage facilities to prevent mold and pest infestations that can lead to increased temperatures.
- Educate Staff: Train farm staff on the importance of maintaining grain storage temperature and how to effectively manage it. This ensures a team-designed approach to quality preservation.
Case Studies on Effective Grain Storage Temperature Management
Several farms and storage facilities have achieved remarkable successes through effective management of grain storage temperature. Here are a few standout case studies:
Case Study 1: Johnson Family Farms
Johnson Family Farms successfully implemented temperature monitoring systems within their grain bins, which allowed them to reduce spoilage incidents by 30%. By conducting regular aeration and leveraging technology, they maintained optimal temperatures throughout their storage season.
Case Study 2: Midwest Grain Supply
Midwest Grain Supply used insulated storage units and fans for aeration, leading to a significant extension of their wheat storage life. Their proactive approach to temperature management resulted in minimal losses during high harvest seasons.
Conclusion
Maintaining the appropriate grain storage temperature is essential for any farm or grain operation aiming to preserve quality and enhance financial performance. With strategies that include temperature monitoring, adjudicating proper aeration, and utilizing advanced technology, farmers can safeguard their investments against spoilage and loss. As trends in agriculture evolve, continually adapting and refining storage practices can lead to further advancements in grain management.
For more in-depth insights and support on grain storage and farm equipment repair, visit TSGC Inc..